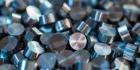
Frequently Asked Questions
General Questions
Since ancient times, humans have found naturally occurring “lodestones” that mysteriously could attract iron and would always point north when suspended in water or hanging from a string. These lodestones came to be called “magnets”, as many of them were found in the Magnesia area of Greece.
Magnets are formed when magnetic materials — certain metals, such as iron, nickel or cobalt — are exposed to a magnetic field. Inside a magnetic field of sufficient strength, groups of atoms within the material, called “domains”, arrange themselves so that they all point in the same direction. Once a majority of the domains is aligned in this way, the metal can be considered a magnet.
In decades past, humans have worked to harness the power of magnetism and create their own magnets. Starting with alnico (Aluminum-Nickel-Cobalt) magnets in the 1930s, magnet producers went on to develop iron-based ferrite magnets in the 1950s. Today’s rare earth magnets were first created in the 1970s — paving the way for magnets to become both smaller and more powerful than ever before.
In addition to the different metals and alloys used to create them, magnets can also be classified into three basic types: temporary, permanent and electromagnets.
Magnetism occurs when a force of attraction or repulsion is exerted between materials like iron, nickel or cobalt. This force is created due to the movement of electric charge within these unique magnetic materials.
We have all observed how magnetic materials attract each other at opposite poles and repel each other at the same pole. However, magnets also possess the ability to transform electrical energy while retaining their own. This allows them to act as a key bridge between mechanical and electrical processes and flows.
Usually, magnets interact in one or more of these four ways:
- Mechanical-to-mechanical: Attracting and repelling objects
- Mechanical-to-heat: Used in hysteresis torque devices and to create eddy currents
- Mechanical-to-electrical: Used in microphones and generators
Electrical-to-mechanical: Used for motors and loudspeakers or other equipment that needs to deflect charged particles
Magnets also can be used to apply magneto-resistance or to create magnetic resonance, such as in MRI devices used in healthcare.
Certain metals are said to be magnetic. The magnetic properties of these metals vary by atomic structure and can be classified in the following basic groups:
Ferromagnetic Metals: The periodic elements Iron (Fe), Nickel (Ni) and Cobalt (Co) are the most common ferromagnetic materials. Due to their unpaired electrons, they can align themselves into a strong magnetic field and retain magnetic properties even after the external magnetic field is removed.
Paramagnetic Metals: Metals such as aluminum, titanium and platinum are called “paramagnetic” because they are attracted to external magnetic fields but cannot retain their magnetic properties once they are removed from those fields. These metals possess unpaired electrons, but their overall atomic structure does not support strong magnetic alignment over time.
Diamagnetic Metals: Gold, silver, copper and most other metals are called diamagnetic, as they are repelled by external magnetic fields. These metals lack the unpaired electrons that promote ferromagnetic or paramagnetic attraction. The behavior of these metals can be overshadowed by other factors, as the diamagnetic behavior is relatively weak in nature.
Metals can exhibit other distinct magnetic behaviors under specific conditions. Some non-magnetic metals become weakly magnetic when sufficiently cooled. Also, combining magnetic and non-magnetic materials together can impart magnetic properties to the finished alloy. This is often seen with steel, as it incorporates both iron (magnetic) and carbon (non-magnetic) within its makeup.
Today’s magnets are made up of different materials, so their manufacturing methods vary. Some of the more common methods include the following:
- Casting & Injection Molding: Materials are melted down and poured or injected into molds to create the desired shape
- Extrusion: Materials are pushed through a die to create the desired shape
- Pressing, Compression Bonding & Sintering: These methods use heat, pressure or some combination of both to create the desired shape
Calendering: The material is passed through special rollers — called “calenders” — to press and smooth it into the desired shape
Types of Magnets
Magnets come in three distinct types: Temporary, Permanent and Electromagnets.
Temporary magnets act like magnets when they are near another substance that emits a magnetic field, but they lose their magnetic characteristics when removed from the field. Soft iron and iron-nickel alloys are often used to create these magnets, since they can be magnetized even within a weaker field. Temporary magnets can be found in everyday items such as telephones and electric motors.
Permanent magnets are so called because they retain their own magnetic field without an external source of magnetism or electricity. Permanent magnets are made from a number of different special alloys:
- Alnico (Aluminum-Nickel-Cobalt): These magnets are often made in bar or rod form and can withstand high temperatures.
- Neodymium-Iron-Boron: Also known as “Neodymium”, “Neo” or “NdFeB”, these rare earth magnets are considered “super magnets” due to their high strength.
- Samarium-Cobalt: Another rare earth alloy used in modern magnets.
- Strontium-Iron: These magnets are also called “Ferrite” or “Ceramic”. They use traditional iron-based alloys.
- Samarium-Ferrite-Nitrogen: So-called “SmFeN” magnets are made from a relatively newer alloy that incorporates rare earth elements to yield high magnetic power.
While these magnets are called “permanent”, they do in fact lose some magnetic power over time. However, this power loss is negligible as long as the magnet is not exposed to high temperatures, power lines or other strong magnets. For example, rare earth Samarium-Cobalt magnets will only lose about 1% power over the space of ten years.
Electromagnets surround a solid metal core with a coil that carries electrical current to produce a magnetic field. These magnets are often used when very high magnetic strength is required. Electromagnets play an important role in motors, telephones, televisions, computers, trains and other devices.
An electromagnet only emits its magnetic field when electrical current is running through it. Removed from a source of power, electromagnets are inert. Permanent magnets retain their magnetic field even if they are removed from an external source.
Rare earth magnets are given that name since their alloys contain one or more of the “rare earth” elements on the periodic table. Rare earth materials have been found to hold exceptionally strong magnetic potential and are often used for modern magnets. The most common rare earth magnets are Neodymium-Iron-Boron (NdFeB) and Samarium-Cobalt (SmCo).
International Magnaproducts Inc. specializes in sourcing and supplying rare earth magnets.
Magnet Strength
Magnetic strength can be measured in a number of ways. A pull force tester applies the magnet to a flat steel plate to measure strength in pounds/kilograms of force exerted. A magnetometer or gaussmeter determines magnetic strength by measuring the surface field in terms of Gauss, Tesla or some other arbitrary unit of measure. Magnetic fluxmeters, permeameters and Helmholtz coils deal with magnetic flux and measure the magnetic “moment” to provide a sense of the magnet’s specific strength and characteristics.
Technically, even permanent magnets in ideal environments lose some strength over time. But the loss is negligible — as little as 1% per decade.
Magnetic materials can weaken or even be rendered inoperable under adverse conditions such as high temperatures, radiation and/or exposure to other strong magnetic fields and electrical currents.
Moisture and humidity can also cause corrosion and harm a magnet’s performance. Magnets expected to operate in humid environments are coated to protect against this.
Shock and vibration should not affect the performance of modern magnets — unless the impact is strong enough to cause breakage or other structural damage.
The strongest magnets are found in the rare earth family. Neodymium (NdFeB) typically yields the strongest magnets. Under high temperature conditions (above 150° C), Samarium-Cobalt magnets have been found to outperform even Neodymium, but this is a niche use case that depends on the specific magnetic circuit.
Magnetic pull force is laboratory measured using a series of attraction tests with steel plates. The peak tensile force measured by these tests is averaged to determine the overall pull force for the magnet.
Pull force measured in the laboratory may not be duplicated under real-world conditions. A magnet with “20-lb pull force” may not be able to hold a twenty-pound object, due to uneven contact, thinner metal, or interference from coatings or rust on the metallic surface.
Customers often want to know “how many Gauss” a magnet has. However, Gauss is a unit of measurement that can express different things. There is no “one true” Gauss measurement for commercial magnets.
Here are two of the most common magnetic properties that can be measured in Gauss:
- Residual Flux Density: Also known as Br — this measurement refers to the amount of magnetic induction that remains in a saturated material once the magnetizing field is removed.
- Surface Field: This measures the magnetic strength on the surface of the magnet itself. Physical shape and material used can affect the surface field strength of different magnets.
As these are two different measurements, it is important to note which Gauss value is in play. A magnet with a Br of 12,300 Gauss will NOT measure 12,300 Gauss on its surface. Surface strength under real-world conditions will also vary based on how far away from that surface the measurement is taken.
International Magnaproducts Inc. includes both the flux density and surface field strength of the different magnets we offer on their respective materials pages.
No. Materials undergoing magnetization reach a “saturation” point. At that point, the material is fully magnetized and cannot be strengthened further.
Generally speaking, a magnetized material can be restored to its original strength, provided it has not been subjected to extreme heat.
Magnetic Fields
A magnetic field is the space where magnetic force is exerted. This field is what causes magnetic repulsion and attraction. A magnetic field’s strength and direction are its two most important characteristics.
Magnetic fields are not visible to the naked eye. However, you can see the outline of a magnet’s field using iron filings. Place the magnet near the filings, and they will reposition themselves as they enter the magnetic field.
A magnetic field weakens dramatically over distance. This decrease in strength is exponential and can be calculated using different equations, depending on the grade, shape and overall physical dimensions of each magnet.
It takes a magnetically attracted material — iron, steel, etc. — to block a magnetic field. Since magnetic fields get weaker over distance, the thickness of the material determines how much of the magnetic field’s power is blocked.
When a magnetic field moves in relation to a conductor, electrical currents called “eddy currents” are formed. Eddy currents create a separate magnetic field that counteracts the relative motion of the original field.
Magnetic Polarity & Flux
Poles are the points where magnetic strength concentrates. Every magnet has a north-seeking and a south-seeking pole, referred to as “North” and “South” for short — since they are drawn to the North and South poles of the Earth itself.
Unless a magnet’s poles have been marked by the manufacturer, you cannot tell the difference between a magnet’s North and South poles with the naked eye. Magnetic north and south can be easily identified with a compass or another magnet with marked poles, however.
You may have heard the saying, “Opposites attract.” This is definitely true for magnets. They attract each other North-to-South and South-to-North. So your compass needle will be drawn to the South pole of a nearby magnet, and two magnets placed near each other will be attracted at opposite poles.
If you try to put two magnets together at their same poles, they will push each other away, North-from-North and South-from-South.
International Magnaproducts Inc. also offers a Magnetic Pole Detector that can be used to quickly and easily identify magnetic poles.
Magnets in a ring shape can be magnetized with one pole on the outside and one on the inside. This is known as radial magnetization. Ring magnets produced in this way are known as unipole magnets (not to be confused with “monopole magnets”).
Radial magnetization only works with ring-shaped magnets. There is no way to produce a disc, cylinder or sphere magnet in this way.
A so-called “monopole” magnet is a magnet with only one pole, i.e. a North pole magnet without a corresponding South or vice versa.
Monopole magnets do not exist in nature and cannot be created by any known means. They are a purely theoretical concept.
You cannot cut a magnet into two pieces in such a way that one piece retains only a North pole while the other has only a South pole. A magnet will always have a North and South pole because of how the magnetic field aligns itself within the material of the magnet.
Magnetic flux is a way of indicating and measuring the behavior of lines of force within a magnetic field. These lines of force are exerted in three dimensions all around the magnet.
Magnetic attraction occurs when these lines of force join up with each other. Magnetic repulsion happens when the lines of force are pushing away from each other.
Magnetic materials need to be magnetized in a particular direction in order to achieve their highest strength. That direction is known as the magnet’s orientation direction, or axis.
Magnets can be magnetized in a different direction than their orientation direction. However, going against the “grain” of the magnet’s axis in this way produces a weaker magnet. These types of magnets are known as “unoriented” or isotropic magnets.
Magnets that have been magnetized in their preferred orientation direction are known as anisotropic. Working with the easiest axis of the magnetic material allows these anisotropic magnets to deliver maximum magnetism.
“Magnetized through thickness” describes the direction of magnetization. Block or disc magnets are magnetized through thickness, so their magnetization runs through the thickest part of the material. When displaying the dimensions for block magnets, IMI always lists thickness last.
Magnetic Characteristics
The three main characteristics you need to know when dealing with magnetic materials are Residual Induction, Coercive Force and Maximum Energy Product.
- Residual Induction (Br): This is a measurement of the magnet’s potential strength, in units of Gauss.
- Coercive Force (Hc): This is a measurement of a material’s ability to retain its magnetism, in Oersted units.
- Maximum Energy Product (BHmax): BHmax provides a measurement of how much volume of magnetic material is needed to produce a defined level of magnetic flux. It is expressed in units of Gauss-Oersted.
These values allow you to compare and contrast different magnetic materials. To compare the amount of magnetic flux at a given distance for two different magnetic materials, divide the larger Br value by the smaller one. The resulting quotient corresponds to how many times greater the flux will be for the higher Br material at the same distance.
Similarly, you can use BHmax to compare the volume of each material necessary to exert the same amount of flux. Divide the larger BHmax value by the smaller one to calculate how many times larger the volume of the lesser material would have to be to match the flux produced by the more powerful material.
A magnet’s effective max temperature is determined by the permeance coefficient (Pc) of its material and by the relative “closed-ness” of the circuit the magnet is operating in. Closed circuits are more stable and are less affected by higher temperatures.
This effective maximum temperature is not to be confused with a magnet’s Curie temperature. Effective maximum is the temperature at which a magnet can operate without losing a functional amount of its magnetism. The Curie temperature reflects the temperature at which a magnet becomes fully demagnetized. The closer to Curie temperature a magnet gets, the more of its magnetism it will lose.
Neodymium Magnets
Neodymium magnets are a type of rare earth magnet, as neodymium is a rare earth element. These magnets are made of a powdered mixture of neodymium, iron and boron that is bonded or sintered to form a magnetic material. Thus, you will also see them referred to as “NdFeB” magnets.
Neodymium magnets are among the strongest magnets available. Their attractive force and ability to retain magnetism make them suitable for just about any application.
Barring exposure to extreme heat or severe structural damage, neodymium magnets do not lose strength at an appreciable rate. This is why neodymium is counted among the “permanent” magnets. They can even be kept with other magnets in an attracting or repelling position without demagnetizing.
In contrast to alnico magnets, neodymium magnets do not require a keeper when not in use.
It depends somewhat on the grade of the magnet. Most standard grade magnets should be kept below 176° Fahrenheit (80°C) to avoid losing magnetic field strength. At the Curie temperature of 590° Fahrenheit (310°C), the magnet will be fully demagnetized.
More precise temperature figures for the magnetic materials IMI sells can be found on their respective Materials pages.
Machining neodymium magnets is a painstaking and potentially dangerous process. The material is extremely brittle and difficult to work with.
Since NdFeB measures RC46 on the Rockwell C scale for hardness, it resists most conventionally available drills and tools. Abrasives, spark machining (EDM) and/or diamond tools are recommended to achieve results when machining neodymium magnets.
Temperature management is important to the process. Tools may overheat and become damaged or unsafe to use, and the high temperature can demagnetize the material itself. The powdered residue generated by machining neodymium is highly flammable as well.
Absolutely not. As mentioned above, intense heat is extremely detrimental to neodymium magnetic materials. Demagnetization is a real risk, and the material itself can even catch on fire if welded or soldered.
In most cases, they should be. Plating helps the iron in the material resist oxidization due to moisture in the air. Even the ambient humidity of most indoor spaces can be enough to damage these magnets if they are left uncoated.
Generally, there are no known health issues working with permanent magnetic fields, including those generated by neodymium magnets. The exception to this rule would be implanted medical devices like pacemakers.
Those who have pacemakers or other medical implants that could be adversely affected by magnets should consult their physician for qualified health advice on working with magnets.
According to the European Parliament’s Restrictions on the Use of Hazardous Substances (RoHS), the following substances are banned from use in modern electrical devices: Cadmium, Lead, Mercury, hexavalent Chromium, PBBs (polybrominated biphenyls) and PBDEs (polybrominated diphenyl ethers).
The neodymium magnets sold by IMI do not contain any of these banned substances and are fully compliant.
Section 1502 of the Dodd-Frank Wall Street Reform and Consumer Protection Act requires that manufacturers report the usage of Columbite-Tantalite, Cassiterite and Wolframite, plus Gold that has been mined in the eastern part of the Democratic Republic of Congo.
Neodymium magnets do not typically contain any of these substances, so they remain unaffected by conflict minerals law in the United States.
Manufacturing & Assembly
Both the Magnetic Materials Producers Association (MMPA) and Magnet Distributors & Fabrications Association (MDFA) have established standards for magnet manufacturing. Both organizations now exist under the umbrella of the International Magnetics Association.
You can access a copy of the MMPA Standard Specification For Permanent Magnet Materials (No. 0100-00) here.
Yes, magnets can be machined. However, hard magnet materials are extremely difficult to machine, unlike flexible or rubber-type magnet materials. Magnets should be machined in the unmagnetized state as much as possible, using waterjet cutting, diamond tools, and/or soft grinding wheels. In general, it is best not to try to machine hard magnet materials unless you are familiar with these specialized machining techniques.
Magnets can be coated or plated to achieve a desired appearance or to suit a particular application. Many magnets now ship from the factory with plating or coating already included, if desired.
We have listed just a few of the most common coatings and plantings below.
Nickel plating is a common choice, especially for Neodymium magnets. What we call “nickel plating” is actually a triple plate consisting of a layer of copper sandwiched between two layers of nickel. Nickel plating is often done to provide corrosion resistance, however, the plating itself is not waterproof.
Nickel plating naturally produces a shiny silver finish. This can be adjusted by the addition of black dye to the outermost layer to produce a darker gray shine. For “gold” plating, a golden finish is added to the standard nickel plate process. Nickel plating can also be painted over to produce a range of other colors. For best results, take specific care to ensure that the paint will adhere properly via sandblasting or other roughing techniques.
Zinc plating can be done to produce a dull, blue-gray appearance. Zinc does not provide the same corrosion resistance as nickel plating. It also leaves behind a black residue that makes it less suitable for use with magnets that are going to be handled regularly.
Epoxy coating provides a plastic finish. An epoxy coating will provide a good degree of resistance to corrosion as long as it remains intact. Epoxy can scratch easily, making it a less durable option than other finishes.
Generally speaking, plating and coating does not adversely affect the strength of a magnet. In some cases, a plastic- or rubber-coated magnet will have lower pull force than an uncoated magnet of the same size and grade. However, this is because the overall volume of magnetic material used is decreased slightly to leave room for the plastic or rubber coating, not because these magnets are made weaker by the coating itself.
If a magnet needs to be fastened or secured, different types of adhesives may be used, depending on the type of magnet.
Conventional hot gluing can be used to attach magnets to cloth, wood, ceramics or other non-metallic substances.
For affixing magnets to metal, conventional epoxies or common hardware adhesives like Gorilla Glue or Liquid Nails can be used.
When attaching nickel-plated magnets, many producers turn to acrylic adhesives made by Loctite. This is a two-part process that calls for an activator or primer in addition to the adhesive itself. Loctite 39205 with the 7380 activator makes for a tight bond, while Loctite 3032 plus primer 770 is another viable option.
A magnetic assembly combines one or more magnets with other components that are intended to influence the functional performance of the magnet(s). These configurations often incorporate steel or other ferrous materials.
The “best” material for a magnet used as part of a motor will depend on the type of motor and the conditions it is intended to work under. As always, the magnetic strength required and overall cost will influence the decision of what magnets to incorporate into a motor.
Ceramic and other ferrite magnets are commonly used for electric motors running on DC current.
For electric cars, Neodymium magnets can be a solid choice, provided that the motor will be sufficiently shielded from high temperatures and environmental corrosion.
When high temperatures are expected, motor manufacturers will turn to Samarium Cobalt (SmCo) magnets due to their reliability under more extreme conditions.
Magnet Safety
Magnets are safe to apply to refrigerators, stoves, ovens and microwaves. They will not affect the function of these appliances.
Some of the more popular grades of stainless steel, such as 304 and 316, do not attract magnets. However, other grades do. Magnetic attraction (and its strength) depends entirely on the specific makeup of the steel alloy.
Legacy media devices like CRT monitors, floppy disks, cassettes, videotapes, and credit cards with magnetic strips can be adversely affected by strong magnetic fields. It is possible to damage or erase these media by exposing them to magnets. More modern devices like flash drives, calculators and cellular phones are generally safe.
In any case, it is better to err on the side of caution and keep your electronics and magnetic materials separate whenever possible.
If you were to place an exceptionally strong magnet directly on top of a computer’s hard drive, it could result in data loss. However, casual exposure to nearby magnets should not cause any damage. Spinning-disc hard drives use powerful magnets of their own, so the threat of magnets erasing people’s computers is somewhat over-exaggerated.
This depends on a lot of factors, but as a general rule of thumb, we recommend keeping the distance between magnets and electronics at four inches plus one inch for every ten pounds of pull force.
IMI is unable to provide comprehensive safety instructions for using magnets around pacemakers. Specific questions about safe operation of pacemakers and other medical devices should be addressed to qualified medical professionals and/or medical device manufacturers.
For consumer warnings and safety issues, IMI recommends taking qualified legal advice from a trusted source. The landscape of different magnets, electronic devices and specific regulations is too complex and varied to provide useful general advice beyond what is provided above.
Shipping & Handling
Always follow basic magnet safety. Avoid getting hands or other extremities caught between powerful magnets. Storing multiple magnets in the “attracted” position can help reduce this risk.
Keeping magnets in closed containers will help prevent them from attracting metal debris like nails or screws.
Do not store magnets near magnetic media and devices such as credit cards, floppy disks and CRT monitors.
For alnico magnets, special care should be taken to prevent demagnetization. These magnets require special keeper plates that attach to each magnet and connect their poles.
When shipping magnets, insert a spacer between each one and wrap them with tape and bubble wrap to prevent collision damage during the shipping process. A rubberized coating will provide an additional layer of protection as well.
Most of the regulatory guidance around shipping magnets pertains to air travel. Per the US Department of Transportation, its Office of Hazardous Materials Safety and the International Air Transport Association, magnets being transported by air cannot exceed a field strength of 0.00525 Gauss when measured at fifteen feet (4.5 meters) from any point on the package. If the package measures more than 0.00525 Gauss at seven feet away (2.25 meters), that package may require a special label to identify it as a dangerous good / magnetic material.
Shipping magnets by ground is not typically bound by such restrictions, making it a viable alternative in most cases.
Dusty magnets can be blown clean with compressed air. Sticky tape also works when compressed air is not available.
It depends on the size of the magnet. Small magnets can be unstuck by hand. Place the magnets in a vertical “stack” and then slide the top one off. The sliding process will help prevent the magnet from immediately snapping back into place — which is always a danger when working with powerful magnets.
For medium-sized magnets, it might be necessary to use the edge of a table of other flat work surface. This time, the magnets should be “stacked” horizontally with the magnet you are trying to remove hanging out past the edge of your work surface. Keeping the rest of the stack secure, press down on the hanging magnet until it releases from the stack.
Large magnets that are two inches or more in size take special care to separate safely. There are dedicated removal tools designed for this purpose that you can order from magnet suppliers or build for yourself using specifications found online.
About IMI
Our facilities are located in Valparaiso, Indiana — right in the heart of the Chicagoland metropolitan area (a.k.a. “The Region”). We are about 51 miles outside of Chicago and 155 miles from Indianapolis.
We are reachable by phone and email. Visit our Contact page to learn more or to get in touch with a specific department.
For over forty years now. We have been part of the magnetics scene since 1983, and our roots extend beyond that to our founder’s previous company, Magnaslice.
We typically have some unplated magnets on offer, but we do not stock them in large quantities, as uncoated/unplated magnets are vulnerable to oxidation. Contact us for specific sizes/shapes/quantities currently available.
You’ve definitely come to the right place. IMI specializes in sourcing and supplying custom rare earth magnets.
Yes, we stock and sell green magnetic viewing paper. Check out our Surplus Materials page for more information.
IMI does not offer a print catalog at this time. All of the most up-to-date information on the magnets we offer can be found here on our website. See our Materials page for more details.
IMI aspires to be your trusted advisor for all things magnetic. In addition to our expert customer service and product support, we offer in-house consulting for engineering and design. We also possess a full range of testing, metrology and reporting services, plus in-house magnetization/demagnetization. We also provide “Just-In-TIme” (JIT) warehousing for our clients.
We partner with offsite providers for welding, coating & plating and laser-engraving services. All of our producers are ISO certified.
Except for certain simple items in small volume, IMI does not do assemblies in house. We will gladly ship to your manufacturing facility or send out to one of our partners for this type of assembly work.
Contact us directly. In addition to your organization’s full contact details for shipping and billing, please provide as much of the following information as possible:
- General application (holding, moving, lifting, etc.)
- Operating temperature range
- Type of magnetic material
- Shape of magnet (disc, ring, block, etc.)
- Dimensions and tolerances (length, width, height, diameter, etc.)
- Strength of holding force (in lbs/kg or Gauss)
- Quantity
- Budget constraints
Yes. Please contact us to begin the process.
We accepts most major credit cards, corporate or personal, as well as ACH and wire transfers. Upon request, we can set up specific credit terms.
We take all possible measures to safeguard your credit card and other personal details you provide us. Contact us for more information.